Fully Functional Miniature Weapon Models Crafted with Exceptional Quality and a Lifetime Service Guarantee
The Pandora’s Box in Your Palm: Why Disassembling Your Miniature Guns Could Be a Costly Mistake
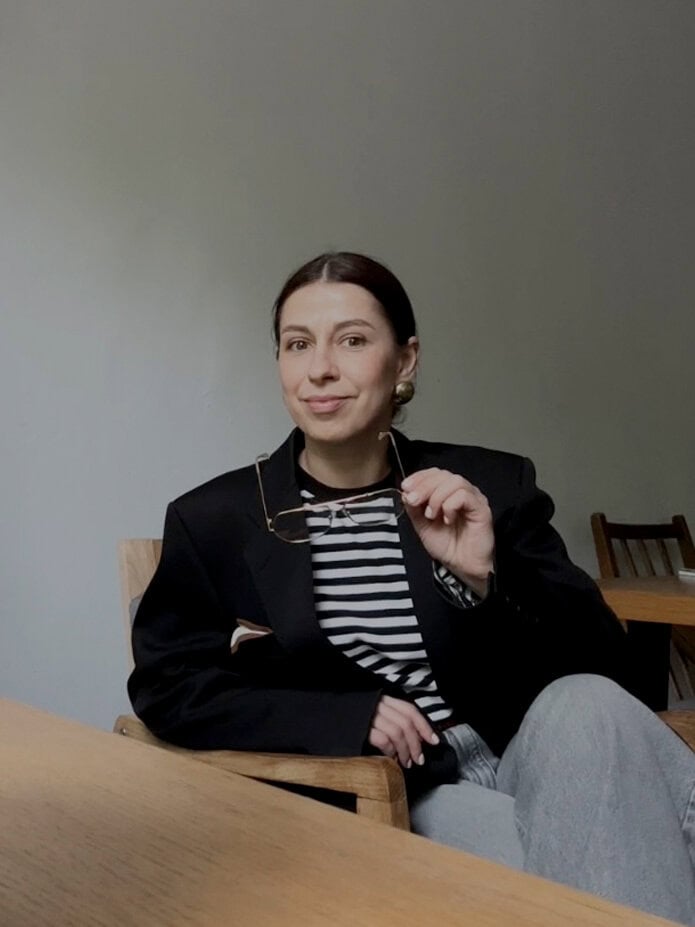
My team and I are actively improving the product listings to provide a better experience for our customers. I’m adding a warning on every platform where I sell miniature pistols, advising not to disassemble them on your own.
Three Obvious Facts
Precision Assembly
In 99.9% of disassembly cases, it gives nothing to the owners. We assemble the model using a microscope, adjusting the parts manually by size. Based on the size of the miniature, even one hundredth of a millimeter matters. It is nearly impossible to repair the model at home.
Disassembly Losses
When disassembling the model, owners lose at least the small springs of the mechanism. Manufacturing these parts for replacement during service only increases the waiting time for customers. Lost parts harm the environment, making us use more materials.
Potential Troubles
Disassembling the model yourself may lead to minor physical injuries, but it is still unpleasant. There was such a case: after shooting, the pin from a pinfire cartridge remained inside, and during disassembly, it sprang out and scratched the pistol’s owner.
I understand that most of my clients are conscious, responsible adults with experience handling real and miniature weapons, some even know how to craft things themselves. Unfortunately, that doesn’t always help avoid unpleasant situations. So, if the issue is more complicated than just tightening a few screws with a small screwdriver, it’s better to
send the malfunctioning model to me for servicing
Our Loyal Promise: Lifelong Support & Wow Moments
On my part, I try to be as loyal as possible. In my nine years of work, I have never refused anyone free service or repairs for my miniatures. Even when all warranty periods have expired, even when parts were lost or severely damaged. Sometimes, I simply send a new miniature instead of the one sent for servicing so that my clients experience a wow effect both during their first encounter with the miniature and in the long-term relationship, as well as from my fatherly, caring service.
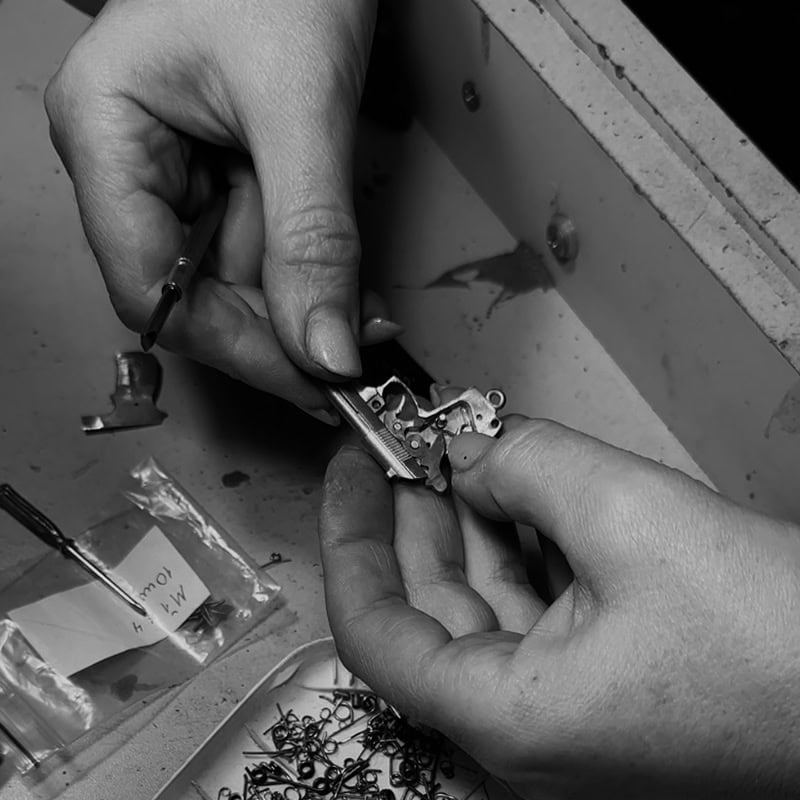
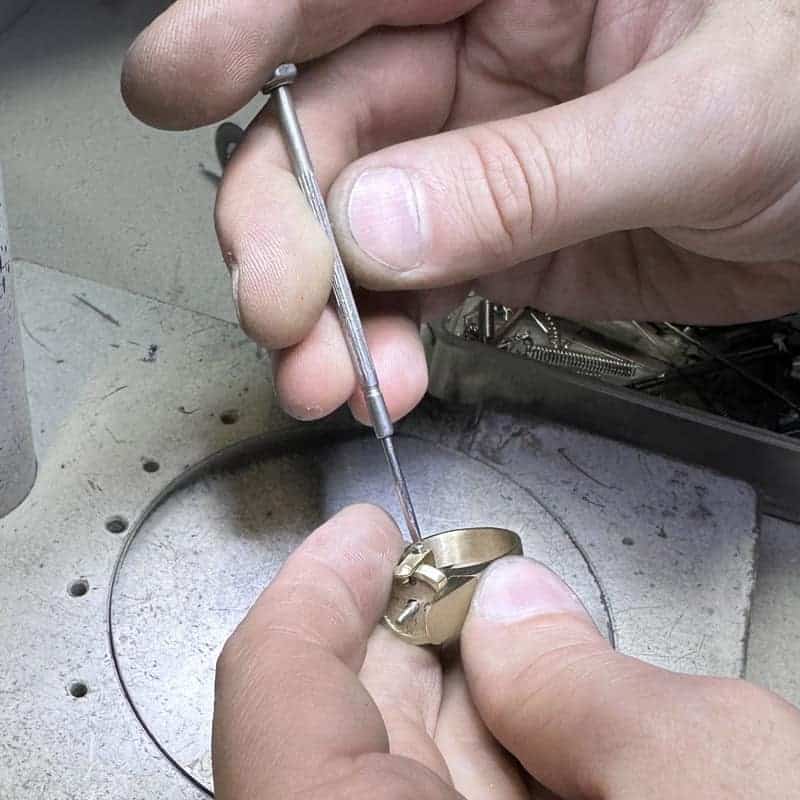
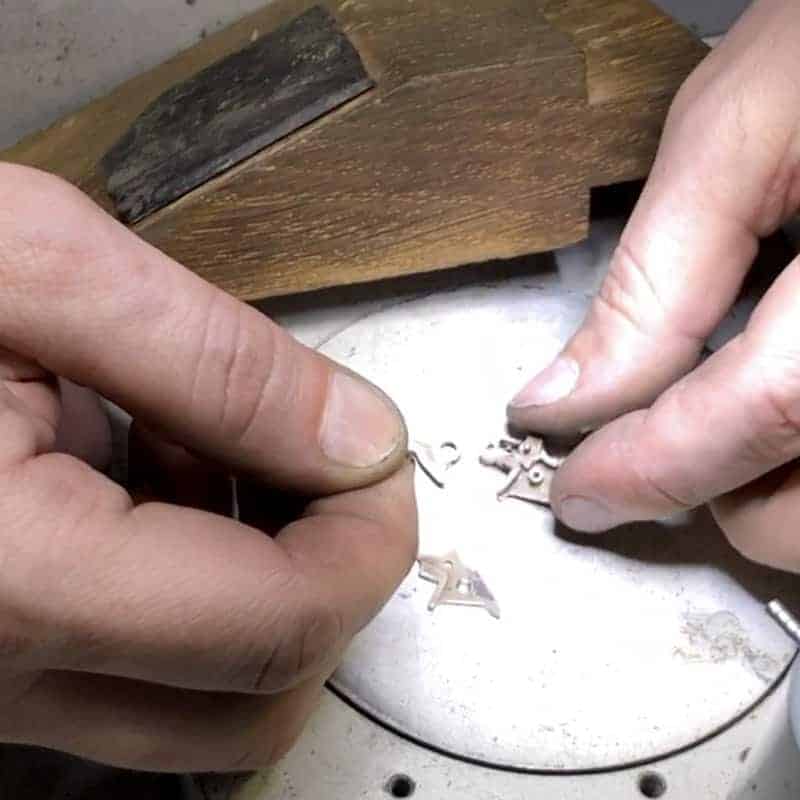
Case 1
Replacing a lost pistol grip pad. Most pads can be easily swapped from one model to another similar model, as their dimensions do not change much during manual adjustment. It is a little more difficult if the screws that hold them are lost. Because the length will have to be adjusted manually. If you are not a problem to cut or grind a small M1.2 stainless steel screw, we will send you the screws and pads for replacement without any issues. We have done this once before.
We have experienced several cases where Ring Gun owners lost the screws that secure the revolver cylinder on top. This is the issue when the model itself provides for unscrewing the screw to remove the revolver cylinder for loading. Therefore, the possibility of easy replacement is conditional and logical here. We just began to make additional screws. We are committed to ensuring your satisfaction, so we will promptly send you a replacement screw for the Ring Gun.
Some problems can be resolved just by tightening the screws that have become loose. For example, the fasteners may loosen over time in models where the barrel is a separate component from the frame, such as in the pinfire Derringer. Recently, we had a Hi-Power in service. In this sample, the bolt would not lock in the loading position. To fix the problem, all we had to do was tighten the screw of the safety catch. Of course, you can do it yourself. And now we will be able to suggest this to customers online.
Well, it is relatively easy to repair the finishes on the models. For blued models, I recommend using Ballistol to spot-restore the black coating. If your models don’t feature bluing, it’s worth considering having them polished by a reputable jeweler you trust. A skilled jeweler can enhance their appearance and bring out their best qualities. Of course, if you do not enjoy bluing yourself or do not have access to a good specialist for polishing products, it is better to send them to me for service.
Thoughts of Experienced Customers
I agree with you 100% that people should never take apart one of your miniature firearms. I know from my own experience that you never take things apart in a miniature. I had a micro miniature calculator made by Casio about 35 years or so. It needed a battery, so I thought I could change it my self. I was wrong, wrong, and wrong! The minute I got the 4 screws, the size of an atom off the calculator. One dropped on the floor, I went to pick it up, and the others landed on the floor and vanished. By now, the calculator was not even made anymore, so into the wastebasket it went! Olha, I am glad a disclaimer is sent with each firearm. You are a very kind and caring owner, and you will replace the lost parts or even the entire miniature if need be. That is doing a thing, very well for your company. It shows you care and have compassion for your customer. But, if this rate of taking apart miniatures, by your customers, grows larger, you may have to enforce the rule of taking apart miniatures. I can see if customers send you the mini with a problem and don’t take it apart. I have learned that many caring, intelligent, and kind people are out there. But some have “Vacancy of the cranium”.
(c) Bill
I completely agree. Although in all my work, there have only been a few odious cases when I was returned miniature guns that looked more like scrap metal.
I once had a 2mm pinfire Вальтер ППК returned, which the owner had tried to smooth with a rough tool, damaging the frame, firing pin, and trigger. The product had deep scratches that could not be repaired by sanding, so all the metal parts had to be replaced.
Recently, there was a case when models with deep scratches were sent for return; the AK-47 had a wooden stock broken into two parts, and the Thompson had a metal barrel completely broken off the frame. Considerable physical force was applied to the models here. After this situation, we implemented a mandatory reminder before returning the models. This reminder emphasizes the importance of packing them securely to prevent the models from shifting inside the box. We aim to avoid receiving mixed wood, metal, and glass fragments.
What did I do in these cases? I made a partial refund for these miniature guns within the framework of what could be rescued and put these customers on the blacklist. I will never not work with them on any project again, as my team’s work deserves respect and appreciation.
What Benefits Do I Get from Providing a Free Service?
Thanks to customers who send miniatures to the service, I have the opportunity to perform my research. I observe how miniatures show themselves over time, identify weak points, find reliable solutions, and can improve the design and technology. For me, this is a way to enhance: make better models that have already become popular, and use the best solutions in new products. And everyone benefits from this, both my company and my customers.
Do not hesitate to contact me if something is wrong with your purchased miniatures.
It is also perfect to reread the instructions for the model and ask me if something is unclear or does not work. Even if you have had experience with real or miniature weapons from other manufacturers, it is not always possible to intuitively understand the principle of operation, especially for intricate designs.
It happens that the model arrives to the client externally undamaged, but during transportation it was shaken and thrown so much that the springs of the mechanism shifted from their place and it stopped working as it should.
Sometimes, everything is fine with the miniature, but something is wrong with the cartridges. The type of cartridges was mixed up, the cartridges got damp during transportation or storage in a wet room, the pin in the cartridge’s pinfire went too deep, and the drummer could not fire it.
In all cases, we ask that you first load according to the instructions. If it doesn’t work, provide a photo or video to understand where the problem is and fix it with minimal effort. Remember—I am with you, and on your side. I want you to enjoy miniatures and life, and I do everything possible to help you do this.

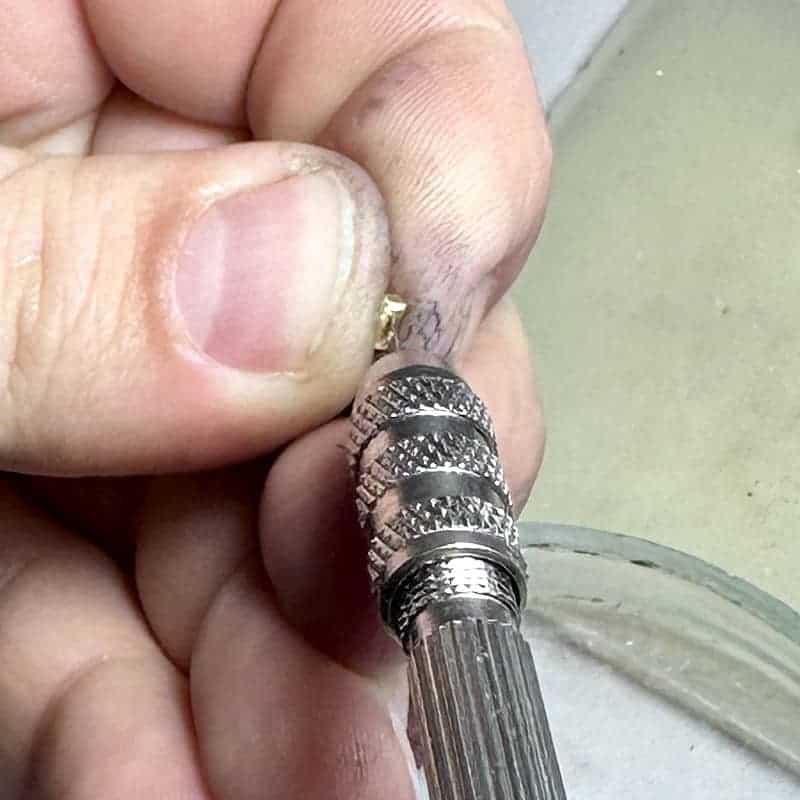
Don’t take miniature guns apart; let everyone do their own job. This will save resources, time, and nerve cells for all of us. It will also give us the opportunity to be even better, to the pleasure of all miniature gun enthusiasts.
Про автора
Мене звати Ольга Полах, і я працюю у виробництві мініатюрної зброї з 2015 року. Я заснувала бренд мініатюрної вогнепальної зброї та з 2016 року веду Instagram-сторінку бренду. Мініатюри бренду користуються популярністю в усьому світі, маючи фанів у 25+ країнах. У 2018 році я стала єдиною власницею бренду та створила велику лінійку мініатюр. Більше 60 моделей мініатюрної зброї з різних історичних періодів було створено. У листопаді 2023 року я дала інтерв’ю Роберту Данну для журналу GunTech, де розповіла про труднощі, з якими я зіткнулася у своєму бізнесі. Також я веду інформаційний бюлетень для клієнтів бренду, який переріс у повноцінний журнал з глибокими статтями, що публікуються на wpolah.com.
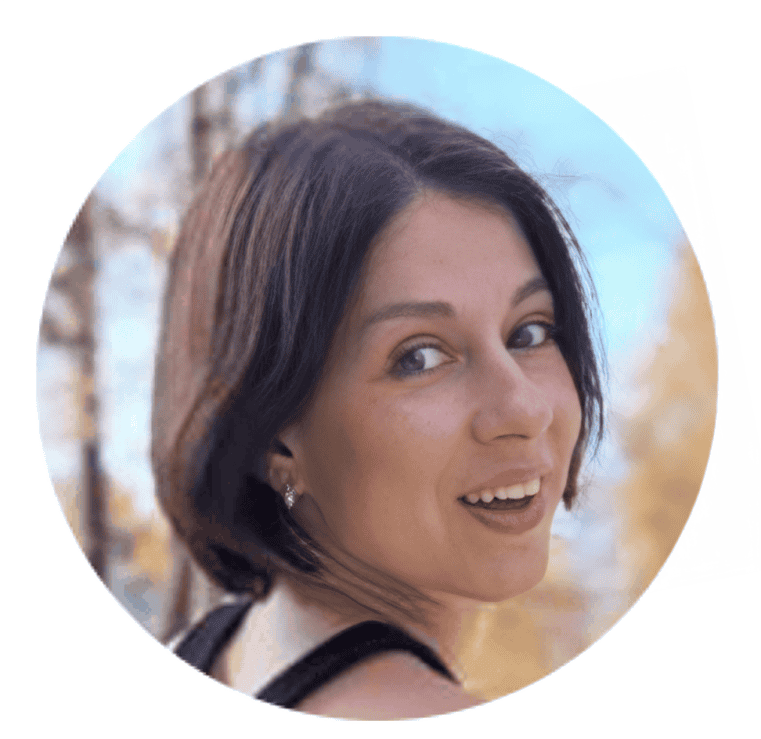
Моя місія — зробити життя людей більш радісним, ділячись цікавими фактами про мініатюрну зброю та надихаючи кожного виражати себе.